From Mold Design to Delivery: Inside Custom Pulp Packaging
Table of contents:
Step-by-Step Breakdown of Molded Pulp Production
How to Design Efficient Custom Molds for Your Product
Working with Manufacturers for Prototyping and Testing
Step-by-Step Breakdown of Molded Pulp Production
Producing custom molded pulp packaging involves a meticulous, multi-step process that ensures durability and eco-consciousness. It begins with selecting the right raw materials.This sustainable base ensures minimal environmental impact. The pulp is then transferred to the molding machine, which, depending on its design, produces various packaging products, ranging from molded fiber egg cartons to protective packaging for electronics. During production, the pulp is vacuum-formed onto precision-crafted molds, ensuring even distribution for durability.Automated drying chambers carefully solidify the forms, ensuring a consistent and durable finish for every item. This precise process guarantees uniformity and quality across all products. Once the drying stage is complete, the items are meticulously trimmed and customized to meet specific client requirements, including size, design, and functionality. The end result is high-quality biodegradable packaging that not only delivers exceptional efficiency but also supports sustainability efforts, making it an eco-friendly solution for modern packaging needs.
How to Design Efficient Custom Molds for Your Product
Designing custom eco-friendly packaging molds requires precision and a focus on sustainability. The first step is understanding the product's specific needs. For example, molded fiber egg cartons require molds that support the delicate nature of eggs while being lightweight. Materials like aluminum are often used for molds due to their durability and ability to endure warehousing or mass production. Collaborate with pulp molding machine manufacturers to ensure that molds are tailored for your required production scale. Your design should prioritize ease of stacking, robustness, and compatibility with automated production. Additionally, incorporating a focus on uniformity and consistency ensures the efficient application of the mold during repetitive runs, enhancing production speed while minimizing waste. Efficient mold designs result in fewer defects, maximizing cost efficiency and environmental care.
Working with Manufacturers for Prototyping and Testing
Prototyping and testing are critical in achieving perfectly tailored products for your sustainable packaging goals. Reaching out to specialized molded pulp manufacturers such as Dwellpac ensures access to precision-engineered prototypes built specifically for industries like food packaging or agricultural supplies. Manufacturers often create prototypes based on your designs and offer sample production runs to test the mold's performance. Testing allows you to evaluate factors like durability, degradation rate in different environments, and overall usability. Transparent communication with your manufacturer is crucial to ensuring that any defects in your product are promptly addressed and necessary refinements are made before production. Clear dialogue allows you to discuss potential challenges, share specific requirements, and align on quality expectations. Additionally, working with manufacturers that have advanced testing facilities offers a major advantage. They can simulate real-world scenarios, such as extreme handling conditions or environmental factors, to ensure your product performs reliably under stress. At the same time, these facilities help verify that your product meets eco-standards, supporting sustainability efforts and aligning with consumer demands for environmentally responsible goods.
Developing an eco-friendly product requires a thoughtful and iterative approach, from design to testing and refinement. By collaborating with experienced manufacturers and leveraging advanced testing facilities, you can ensure the quality and sustainability of your final product. Transparent communication and a commitment to addressing challenges are key to achieving a design that meets environmental standards while delivering reliable performance. With these steps, you can create solutions that not only benefit your customers but also contribute positively to the planet.
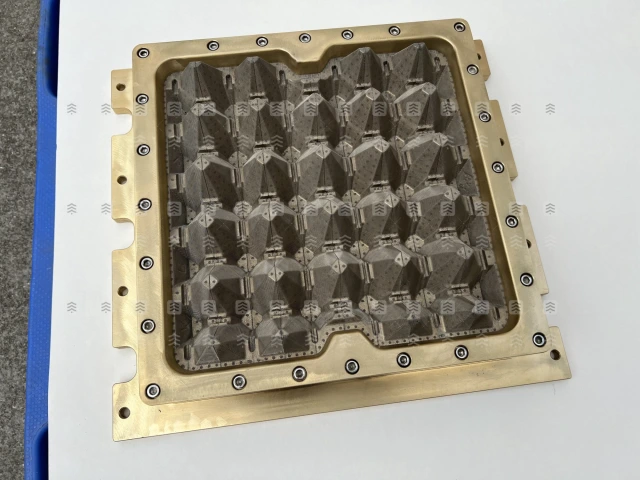
Comments
Post a Comment