The Role of Cable Lugs in High-Voltage Applications and Safety Considerations
Table of contents:
Design Features of Cable Lugs for High-Voltage Systems
Material Selection: Ensuring Durability Under High Stress
Safety Standards and Compliance for High-Voltage Cable Lugs
Case Studies: Successful Implementation in High-Voltage Projects
Design Features of Cable Lugs for High-Voltage Systems
Cable lugs are specially designed to handle the unique demands of high-voltage systems. Their primary role is to securely connect cables to terminal points, facilitating the smooth transmission of power. High-voltage cable lugs are engineered to withstand extreme electrical stress, as well as environmental factors such as temperature fluctuations and potential corrosion. A prominent example is the 66KV 800sq. oil-blocking copper terminal, which employs features like tinning and pickling to enhance its anti-oxidation and corrosion resistance. These design features not only ensure optimal electrical conductivity but also contribute to the long-term durability of the system. For instance, high-grade materials like T2 copper, combined with surface treatments of tin plating, improve conductivity while preventing degradation caused by environmental exposure. Additionally, mechanical tensile load tests further verify these lugs' crimping performance and strength under operational stress.
Material Selection: Ensuring Durability Under High Stress
Material choice is a critical factor in the performance of high-voltage cable lugs. Most premium cable lugs, such as copper cable lugs, are constructed from T2 copper for its exceptional conductivity, thermal performance, and resistance to wear over time. High-voltage applications subject cable connectors to intense mechanical and electrical loads. By using annealing treatments, manufacturers like cable lugs supplier optimize the structural and crimping performance of copper cable lugs. Tin plating, an additional feature commonly employed, protects the copper from oxidation and maintains conductivity over extended periods. Materials and surface treatments that enhance resistance to oxidation and corrosion are especially valuable in outdoor applications, where exposure to moisture and air pollutants is frequent. This durability ensures minimal energy loss and increases the overall efficiency and safety of the high-voltage system.
Safety Standards and Compliance for High-Voltage Cable Lugs
High-voltage cable lugs must adhere to strict safety standards to minimize risks such as electrical faults, overheating, or equipment failure. Standards like GB/T 14315-2008 provide essential guidelines for the design, manufacturing, and quality assurance of cable lugs in high-voltage applications. Products such as the 66KV 800sq. oil-blocking copper terminal undergo rigorous testing, including mechanical tensile load assessments, to verify their reliability in terms of crimping strength and operational performance. Ensuring compliance with these standards helps manufacturers align products with regulatory requirements and boosts user confidence in the safety of their systems. Furthermore, modern manufacturing processes incorporate extensive testing by national power equipment safety bodies, ensuring that standards are not only met but exceeded. Enterprises that rely on suppliers adhering to these guidelines can mitigate operational risks while upholding the safety of their personnel and equipment. Using compliant products also helps organizations avoid penalties and improve long-term operational efficiency.
Case Studies: Successful Implementation in High-Voltage Projects
Real-world scenarios demonstrate how robust cable lugs have significantly improved the efficiency and safety of high-voltage systems. For example, numerous high-voltage power stations worldwide rely on products like the 66KV copper core oil-blocking terminals to maintain stable and efficient operations. By integrating cable connectors tested for tensile strength and corrosion resistance, these facilities have minimized energy loss and prevented catastrophic equipment failures. Another example is large-scale infrastructure projects where cable lugs supplied by top-tier cable lugs manufacturers provided the backbone for reliable power distribution. These terminals effectively reduced downtimes caused by wear and tear, optimizing maintenance schedules and lowering operational costs. Such implementations prove that selecting the right cable lugs is not just an operational necessity but also a strategic advantage for any enterprise managing high-voltage power systems.
High-voltage systems require components that can perform reliably under immense stress, and cable lugs are at the forefront of ensuring these systems operate safely and efficiently. By focusing on high-quality materials like T2 copper, incorporating design features that enhance durability, and complying with safety standards, manufacturers are paving the way for advancements in electrical infrastructure. Whether you are an industry professional or a decision-maker in power distribution, partnering with a reliable cable lugs supplier will ensure your operations meet their safety and efficiency goals. If you’re looking to explore premium-grade copper cable lugs for your high-voltage needs, consider offerings such as the 66KV 800sq. oil-blocking copper terminal from trusted suppliers like HCDQTech. With tested reliability and a commitment to quality, these products deliver solutions tailored for the most demanding environments. Reach out today to learn how these innovative solutions can bolster your high-voltage projects.
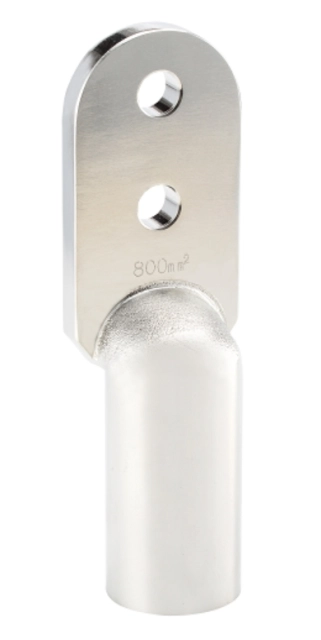
Comments
Post a Comment