Maintenance and Storage of Grinding Wheels
Grinding wheels play a pivotal role in the metal fabrication and construction industries, ensuring efficient and precise material removal. Whether you are sourcing grinding wheels from a trusted grinding wheels supplier, investing in quality tools like a 4” cut-off wheels manufacturer or a 7” grinding wheels manufacturer, proper maintenance and storage are non-negotiable to maximize utility, ensure safety, and extend their lifespan. Just like other industrial tools, grinding wheels require careful handling and proactive upkeep. Below, we explore the practices that keep grinding wheels in optimal condition for continued performance.
Table of contents:
Proper Handling to Prevent Damage and Ensure Safety
Storage Conditions to Maintain Wheel Integrity
Regular Inspection Procedures for Wear and Defects
Guidelines for Dressing and Truing Grinding Wheels
Proper Handling to Prevent Damage and Ensure Safety
The durability and efficiency of grinding wheels highly depend on how they are handled. An indispensable rule when handling grinding wheels is to avoid dropping or subjecting them to impact. Since they are meticulously engineered for precision tasks, even minor cracks or chips could compromise their integrity, which creates a safety hazard during use. Always transport grinding wheels individually in protective packaging and store them in a designated area. Users should also avoid using the sides of the grinding wheels for operations unless they are specifically designed for side grinding, as per the recommendations from abrasives grinding wheels suppliers, to minimize risks. Additionally, ensure that operators are trained to handle grinding wheels safely and that personal protective equipment (PPE), such as goggles and gloves, is always employed during operations.
Storage Conditions to Maintain Wheel Integrity
Improper storage is one of the primary causes of grinding wheel degradation. Grinding wheels should always be stored in a cool, dry place away from extreme humidity or temperature fluctuations. Excessive moisture can weaken the wheel bond, and high temperatures can damage the resin bond, affecting its effectiveness. Most professional grinding wheels suppliers recommend storing the wheels horizontally and avoiding stacking them unevenly to prevent warping. Ensure that your storage racks are designed to support the wheel’s diameter securely. Access to the wheels should also be controlled to prevent unauthorised personnel from mishandling these essential tools. The message is simple—your storage method directly correlates to their operational reliability and longevity.
Regular Inspection Procedures for Wear and Defects
Regular inspections are essential since grinding wheels naturally wear down after repeated use. Before use, ensure each grinding wheel is thoroughly examined for visible signs of wear, cracks, or chips. A “ring test” is a quick and effective method to check for wheel integrity. Lightly tap the wheel with a non-metallic object, such as a wooden dowel or plastic ruler; an intact wheel produces a clear ringing sound, while a damaged wheel will generate a dull tone. Always check the manufacturer guidelines from the best angle grinder wheels for cutting metal to know when replacements are necessary. Inspections must also extend to verifying whether the wheel RPM matches the grinder's maximum rated speed. Using incompatible tools is a safety risk that no operator or business should undertake. Implementing a proper inspection routine could significantly minimize safety incidents and workflow disruptions.
Guidelines for Dressing and Truing Grinding Wheels
Proper dressing and truing are vital steps in ensuring grinding wheel efficiency. Dressing removes embedded material on the grinding wheel, restoring its sharpness and maintaining proper grain exposure. On the other hand, truing corrects any measurement inaccuracies, ensuring the wheel rotates evenly. Both procedures prolong grinding wheel performance and result in smoother finishes. Always use a diamond dressing tool to perform these maintenance steps accurately. Guidelines should consider the type of grinding wheel in use, as tools sourced from premium 4” cut-off wheel manufacturers may have specific maintenance instructions tailored to their product lines. Furthermore, a standardized schedule for dressing and truing should be instituted for heavy-use operations. Operators must ensure these procedures are consistent with manufacturer instructions provided by trusted abrasives grinding wheels suppliers and adhere to approved maintenance equipment.
Adherence to these best-practice maintenance steps doesn't just ensure optimal grinding wheel performance but also maximizes workplace safety and operational efficiency. Whether you’re in the market for top-quality tools from a reliable 7” grinding wheels manufacturer or regular replacements from an abrasives grinding wheels supplier, meticulous maintenance is the critical final step in guaranteeing reliable, long-term use. One action you can take today? Evaluate your current grinding wheel handling and storage systems to pinpoint areas for improvement. Secure a seamless production line with well-maintained grinding wheels that deliver superior results.
Searching for high-quality grinding wheels that will elevate your operations? Explore the trusted selection at Fuji Grinding Wheel, a leader in the industry delivering durable solutions without compromise. Visit our website today and request a quote now to see how we can meet your grinding needs efficiently!
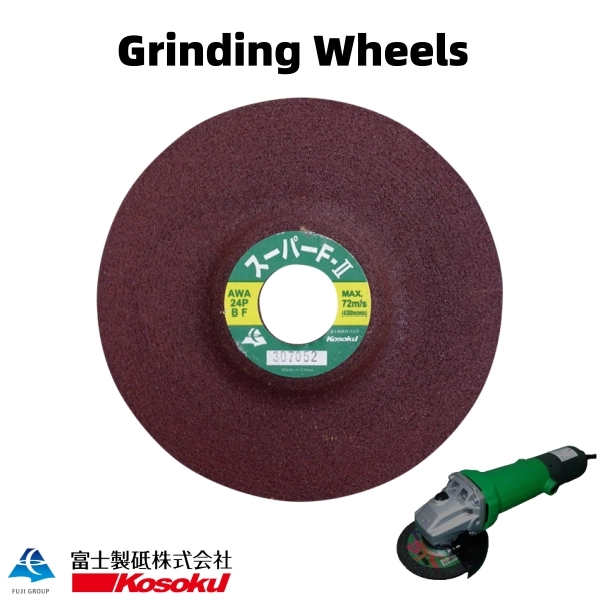
Comments
Post a Comment