Crafting the Future with Hot Press Forming in Composite Manufacturing
The world of composite manufacturing is evolving rapidly, and at the heart of this revolution is hot press forming technology. This process not only elevates the quality and performance of composite materials but also paves the way for innovative applications in industries such as aerospace and automotive. Let's explore why hot press forming is a game-changer and how it is shaping the future of high-performance composites.
Table of contents:
Why Hot Press Forming Is Optimal for Creating Durable Composite Materials
Key Applications of Hot Press Forming in Aerospace and Automotive Composites
How Hot Press Forming Improves Composite Strength, Weight, and Precision
Top Features to Look for in Composite-Optimized Hot Press Forming Equipment
Why Hot Press Forming Is Optimal for Creating Durable Composite Materials
Hot press forming stands out as an optimal method for creating durable composite materials due to its ability to provide superior strength and precision. By using high temperatures and pressure, this technique ensures that composite layers are perfectly bonded, resulting in materials that can withstand significant stress and environmental challenges. The process allows for the creation of lightweight yet robust components, making it ideal for applications that require both strength and reduced weight.In addition to strength, hot press forming offers enhanced precision in the shape and dimensions of composite parts. This is crucial for industries where exact specifications are necessary to ensure safety and efficiency. The ability to produce parts with consistent quality and uniformity is a testament to the reliability of hot press forming in composite manufacturing.Furthermore, hot press forming is known for its efficiency. The process is relatively fast, reducing production time and lowering costs. This makes it an attractive option for manufacturers looking to optimize their operations while maintaining high standards of quality.
Key Applications of Hot Press Forming in Aerospace and Automotive Composites
In the aerospace industry, the demand for materials that offer high strength-to-weight ratios is paramount. Hot press forming is utilized to manufacture components that meet these requirements, contributing to the development of lighter aircraft that consume less fuel and reduce emissions. The precision of hot press forming also ensures that aerospace parts meet stringent safety and performance standards.Similarly, the automotive sector benefits from hot press forming technology in the production of lightweight vehicle components. This not only enhances fuel efficiency but also improves vehicle handling and performance. The ability to produce complex shapes with high precision is particularly valuable in the automotive industry, where aesthetics and aerodynamics play significant roles.Beyond these industries, hot press forming is also finding applications in other fields such as construction and renewable energy. Its versatility and effectiveness make it a key player in the advancement of composite materials across various sectors.
How Hot Press Forming Improves Composite Strength, Weight, and Precision
The advantages of hot press forming extend beyond mere durability. This technique significantly improves the strength, weight, and precision of composite materials. By ensuring that each layer of the composite is thoroughly bonded, the resulting material exhibits exceptional tensile strength and resistance to wear and tear.In terms of weight, hot press forming allows for the production of lightweight composites without compromising on performance. This is crucial in industries where every gram matters, such as aerospace and automotive, where reducing weight can lead to significant improvements in efficiency and cost-effectiveness.Precision is another hallmark of hot press forming. The process allows manufacturers to produce parts that meet exacting specifications, ensuring that each component functions as intended. This is particularly important in applications where precision is critical to the overall performance and safety of the product.
Top Features to Look for in Composite-Optimized Hot Press Forming Equipment
When selecting hot press forming equipment for composite manufacturing, several key features should be considered. These include precision control systems that allow for accurate temperature and pressure adjustments, ensuring optimal bonding and material properties. Equipment that offers digital monitoring and control capabilities can enhance the efficiency and reliability of the manufacturing process.Additionally, look for equipment that supports a wide range of materials and configurations. This flexibility allows manufacturers to experiment with different composite formulations and expand their product offerings. Finally, consider equipment that emphasizes energy efficiency and sustainability, aligning with current industry trends toward environmentally responsible manufacturing practices.
In conclusion, hot press forming is revolutionizing the field of composite manufacturing. Its ability to produce durable, lightweight, and precise components makes it indispensable in industries such as aerospace and automotive. By understanding the benefits and applications of this technology, manufacturers can better harness its potential to create high-performance composites that meet the demands of modern engineering.For those interested in exploring the capabilities of hot press forming further, consider reaching out to experts or investing in state-of-the-art equipment that can elevate your manufacturing processes. The future of composite manufacturing is bright, and hot press forming is leading the way.
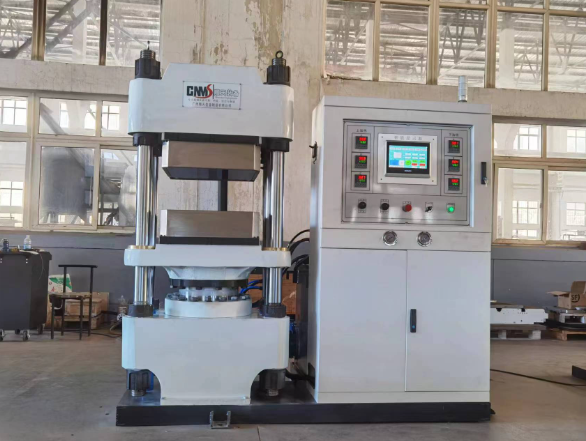
Comments
Post a Comment