Maximizing Durability with Electroless Nickel Plating: A Deep Dive into Wear Resistance
Industrial components endure significant wear and tear in their daily use. Whether subjected to constant movement, harsh chemicals, or mechanical impact, the longevity of these parts can directly affect the productivity and costs of a business. That's where electroless nickel plating equipment comes into play, offering a powerful solution to enhance surface durability. This article explores six key areas where electroless nickel plating delivers superior wear resistance, providing a comprehensive understanding of why it's the go-to choice for industries worldwide.
Table of contents
Surface Hardness
One of the most important benefits of electroless nickel plating is the increase in surface hardness. Hardness levels can range from 550 HV to 1000 HV, depending on whether the coating undergoes heat treatment. This elevated hardness improves the resistance of components to scratching and mechanical damage, especially in high-friction environments. For industries where parts experience heavy usage, the enhanced hardness provides a durable surface capable of withstanding repetitive wear without losing integrity. In applications where the material's structural strength needs to be preserved, such as in aerospace or electronics, the uniformity of the plating allows for an increase in durability without altering the component's original characteristics.
Abrasion Resistance
Abrasion is one of the most common causes of damage in mechanical parts. Components subjected to constant friction or movement often experience a gradual breakdown of their surface, leading to reduced performance and eventual failure. Electroless nickel plating offers a high level of abrasion resistance, shielding parts from wear caused by repetitive motion. This makes it particularly useful in high-friction environments. The uniformity of the coating provided by electroless nickel plating ensures that every area of the component, even those hard-to-reach places, receive consistent protection, reducing the risk of weak spots or premature failure.
Adhesion Strength
Durability also relies on the strength of the bond between the plating and the substrate. Electroless nickel plating offers exceptional adhesion strength, ensuring that the coating remains firmly attached to the base material. This robust bonding is crucial in preventing the coating from chipping or peeling off under mechanical stress or wear. With adhesion strengths reaching up to 450 MPa, the bond between the plating and the material remains intact even under high-stress conditions.
Chemical Resistance
In industries where components are exposed to harsh chemicals, maintaining the integrity of the surface is crucial for performance. Electroless nickel plating provides excellent chemical resistance, allowing parts to withstand exposure to corrosive environments without degradation. This is particularly valuable in chemical processing plants, marine applications, or environments where parts come into contact with solvents, acids, or salts. The phosphorus content in the nickel coating enhances its ability to resist corrosion, making it an ideal solution for parts that need to function reliably in harsh environments. This resistance not only extends the component's lifespan but also reduces the need for frequent replacements, saving businesses both time and money.
Fatigue Resistance
Another critical factor contributing to durability is fatigue resistance. Components subjected to repeated stress can develop cracks or other forms of structural damage over time. Electroless nickel plating helps mitigate this issue by adding a protective layer that absorbs some of the mechanical stress. This reduces the likelihood of fatigue cracks forming, particularly in parts used in high-stress environments like aerospace, automotive, and heavy machinery. By enhancing the material's ability to endure repeated cycles of stress, electroless nickel plating ensures that parts maintain their structural integrity over a longer period, significantly extending their operational lifespan.
Impact Resistance
In environments where parts are subjected to mechanical shocks or sudden impacts, impact resistance becomes essential. Electroless nickel plating creates a uniform, dense layer of protection that helps distribute the force of an impact across the entire surface, reducing the risk of localized damage. Industries such as mining, construction, and defense can greatly benefit from the impact resistance provided by electroless nickel plating. The coating ensures that components remain operational even after sudden or repeated impacts, reducing downtime and maintenance costs.
For businesses seeking to enhance the durability of their industrial components, investing in electroless nickel plating equipment is a smart move. By improving surface hardness, abrasion resistance, adhesion strength, chemical resistance, fatigue resistance, and impact resistance, this surface treatment technology provides comprehensive protection that extends the lifespan of treated parts. As industries continue to push the boundaries of performance and efficiency, ensuring that components are built to last is more important than ever. If you're looking to invest in high-quality surface treatment equipment, visit fengfantrade.net to learn more about how electroless nickel plating can benefit your operations.
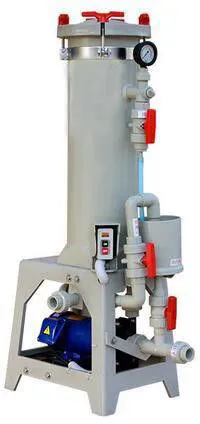
Comments
Post a Comment