Mastering Precision Manufacturing with 0.8mm Stamping Molds
In the world of manufacturing, precision is key. But achieving high accuracy often comes with challenges. Enter the innovation of 0.8mm stamping molds, which promise to revolutionize precision manufacturing. If you're a business professional or a manufacturer, understanding the power of these molds can elevate your production process. Let's explore why 0.8mm stamping molds are a game-changer and how they can enhance your operations.
The Role of Thickness in Stamping Mold Performance
Achieving High Precision with 0.8mm Stamping Molds
How Thin Molds Improve Production Efficiency
The Role of Thickness in Stamping Mold Performance
Thickness plays a crucial role in stamping mold performance. The thickness of the mold determines its durability, flexibility, and ability to produce high-precision parts. Thinner molds, like the 0.8mm variety, offer unique advantages over their thicker counterparts. They allow for more intricate designs and finer details, which are essential in industries requiring high precision, such as electronics and automotive manufacturing. By reducing the thickness of the mold, manufacturers can achieve tighter tolerances and more consistent results. This leads to fewer rejects and less rework, ultimately saving time and resources. Additionally, thinner molds can better handle complex geometries and delicate materials, making them ideal for producing small, high-precision components. In summary, the thickness of a stamping mold directly impacts its performance and the quality of the finished product. Thinner molds offer greater precision, making them a valuable asset in high-tech manufacturing environments.
Achieving High Precision with 0.8mm Stamping Molds
High precision is the hallmark of successful manufacturing. 0.8mm stamping molds are designed to meet the stringent demands of modern production lines. These molds are manufactured using advanced techniques and materials, ensuring they can withstand the rigors of high-volume production while maintaining accuracy. One of the key benefits of 0.8mm stamping molds is their ability to produce parts with exceptional detail and consistency. This level of precision is achieved through meticulous design and engineering, which allows for the creation of intricate patterns and shapes. The use of high-quality materials also ensures that the molds remain stable and reliable, even under continuous use. Furthermore, 0.8mm stamping molds are versatile and can be used in various applications. From electronic components to automotive parts, these molds are capable of producing a wide range of products with unparalleled precision. This versatility makes them an invaluable tool for manufacturers looking to enhance their production capabilities and stay ahead of the competition.
How Thin Molds Improve Production Efficiency
Efficiency is a critical factor in manufacturing, and thin molds like the 0.8mm variety play a significant role in improving it. By reducing the material thickness, these molds require less force to operate, which translates to lower energy consumption and reduced wear on equipment. This, in turn, leads to longer tool life and lower maintenance costs. In addition to energy savings, thin molds also contribute to faster production cycles. The reduced thickness allows for quicker cooling and solidification of the stamped material, resulting in shorter cycle times. This increased speed can significantly boost overall productivity, allowing manufacturers to meet tight deadlines and increase output without compromising quality. Finally, the use of 0.8mm stamping molds can lead to cost savings in material usage. Thinner molds generate less scrap and waste, which not only reduces material costs but also minimizes the environmental impact of the manufacturing process. This aligns with the growing trend toward sustainable manufacturing practices, making 0.8mm stamping molds an eco-friendly choice for forward-thinking businesses.
In conclusion, 0.8mm stamping molds are a powerful tool for achieving high precision and efficiency in manufacturing. Their ability to produce intricate designs with consistency makes them ideal for various applications, while their thin profile contributes to energy savings and faster production cycles. By investing in these advanced molds, manufacturers can enhance their operations, reduce costs, and stay competitive in an increasingly demanding market.
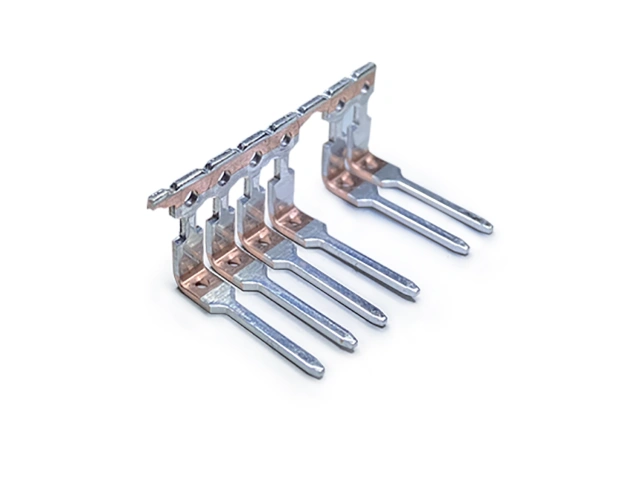
Comments
Post a Comment