How Vacuum Casting with Silicone Molds Revolutionizes Manufacturing
In the world of manufacturing, innovation is the key to staying ahead. One such groundbreaking advancement that is transforming the industry is vacuum casting with silicone mold. This technology has not only revolutionized the way prototypes are made but has also paved the way for more efficient production methods. This blog post will explore the intricacies of vacuum casting, its advantages, and practical applications, providing you with valuable insights into how this technique is reshaping manufacturing.
Understanding the Vacuum Casting Process with Silicone Molds
Key Advantages of Vacuum Casting for Rapid Prototyping
Comparing Vacuum Casting to Traditional Manufacturing Methods
Case Studies: Successful Applications of Vacuum Casting Silicone Molds
Tips for Maximizing Efficiency with Vacuum Casting Technology
Understanding the Vacuum Casting Process with Silicone Molds
Vacuum casting is a process that uses a vacuum to draw liquid material into a mold, typically made from silicone. The process begins with the creation of a master model, which is often produced using 3D printing technology. This master model is then encased in liquid silicone, which cures to form a durable mold. Once the mold is ready, it is used to cast parts by pouring liquid material into it under vacuum conditions. This ensures that the material fills every nook and cranny of the mold, resulting in highly detailed and precise replicas of the master model. The versatility of silicone molds makes them ideal for producing complex geometries and intricate details that would be challenging to achieve with traditional methods.
Key Advantages of Vacuum Casting for Rapid Prototyping
One of the primary benefits of vacuum casting is its suitability for rapid prototyping. This method allows for the quick and cost-effective production of high-quality prototypes, making it an invaluable tool for product development. Unlike injection molding, which requires expensive tooling and longer lead times, vacuum casting can produce parts in a matter of days. This speed and efficiency enable engineers and designers to iterate rapidly, testing and refining their designs with minimal delay. Additionally, vacuum casting with silicone molds offers excellent material versatility. A wide range of materials can be used, including polyurethane and epoxy resins, which mimic the properties of production-grade plastics. This allows for the creation of functional prototypes that closely resemble the final product in terms of appearance and performance.
Comparing Vacuum Casting to Traditional Manufacturing Methods
When compared to traditional manufacturing techniques, vacuum casting stands out for several reasons. Firstly, it is much more cost-effective for low to medium volume production runs. The initial costs associated with creating silicone molds are significantly lower than those for metal tooling used in injection molding. This makes vacuum casting an attractive option for startups and small businesses looking to produce limited quantities of parts without breaking the bank. Secondly, the precision and detail achievable with vacuum casting are unparalleled. The use of vacuum ensures that the liquid material fills the mold completely, eliminating air bubbles and defects that can compromise the quality of the final product. This level of accuracy is particularly beneficial for industries such as medical devices and electronics, where precision is paramount.
Case Studies: Successful Applications of Vacuum Casting Silicone Molds
Several companies have successfully leveraged vacuum casting to bring their innovative products to market. For instance, custom service plastics have utilized this technology to produce intricate components for various applications. By employing vacuum casting, they have been able to achieve exceptional detail and accuracy, resulting in high-quality parts that meet stringent industry standards. Another notable example is the use of vacuum casting in the automotive industry. Manufacturers have employed this technique to create prototypes of complex engine components and interior parts. The ability to produce highly detailed prototypes quickly has allowed them to accelerate the development process and bring new models to market faster.
Tips for Maximizing Efficiency with Vacuum Casting Technology
To fully capitalize on the benefits of vacuum casting, there are several best practices to keep in mind. First and foremost, it is crucial to select the right material for your application. Different materials offer varying properties, so it is essential to choose one that aligns with your specific requirements. Additionally, ensuring proper mold maintenance is vital for consistent results. Regularly cleaning and inspecting molds will help prolong their lifespan and maintain the quality of the cast parts. Another tip is to optimize the vacuum casting process by fine-tuning parameters such as temperature and pressure. Experimenting with these variables can help achieve the desired level of detail and precision in the final product.
In conclusion, vacuum casting with silicone molds is a revolutionary technology that is transforming the manufacturing landscape. Its ability to produce high-quality prototypes quickly and cost-effectively makes it an invaluable tool for product development. By understanding the intricacies of the vacuum casting process and leveraging its advantages, businesses can streamline their production processes and bring innovative products to market faster. If you are looking to explore the potential of vacuum casting for your projects, consider partnering with experts in custom service plastics who can guide you through the process and help you achieve exceptional results.
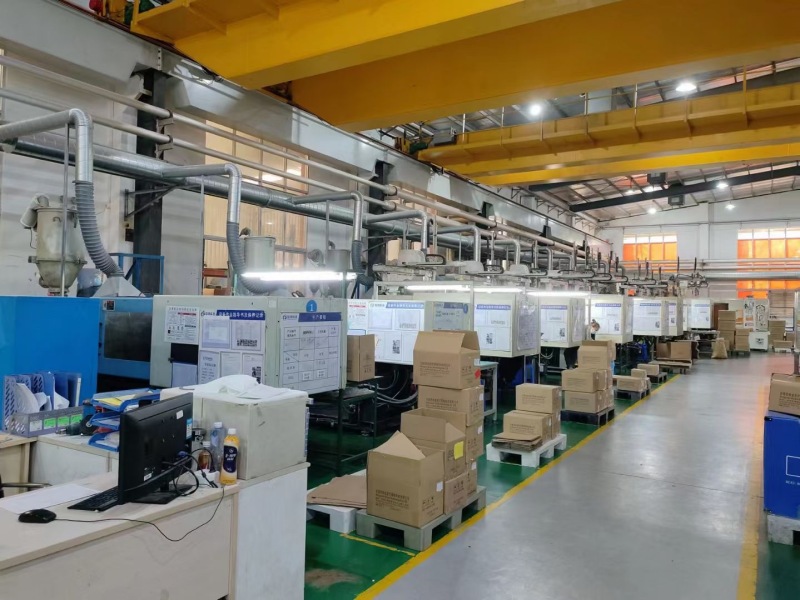
Comments
Post a Comment