Customizing CNC Machining Services for Your Needs
In the world of manufacturing, customization can be the difference between success and mediocrity. Personalizing CNC machining services to meet specific needs allows businesses to achieve exceptional precision, quality, and functionality in their products. This blog post will guide you through the benefits of tailored CNC machining solutions, how to order custom CNC machining services, real-life examples of customized machining projects, and expert tips for collaborating with CNC machining service providers. By the end, you’ll see just how crucial customized CNC machining can be for your business.
The Advantages of Tailored CNC Machining Solutions
Step-by-Step Guide to Custom CNC Machining Orders
Real-Life Examples Customized Machining Projects
Enhancing Product Design with Custom CNC Machining
Expert Tips for Collaborating with CNC Machining Service Providers
Understanding Different CNC Machining Techniques
Selecting the Right Materials for Your CNC Machining Project
Ensuring Quality Control in Custom CNC Machining
The Role of Surface Finishing in Custom CNC Machining
The Future of Custom CNC Machining
The Advantages of Tailored CNC Machining Solutions
When it comes to manufacturing, one size rarely fits all. Custom CNC machining services offer a variety of advantages that cater to the unique needs of each project. The ability to specify materials, dimensions, and design intricacies ensures that the final product meets exact specifications. This level of customization also allows companies to produce parts with tighter tolerances and improved performance. Furthermore, custom solutions reduce waste and inefficiencies, leading to cost savings in the long run. Whether you need precision metal parts for aerospace applications or customized components for consumer electronics, tailored CNC machining services can help you achieve the perfect fit for your project.
Step-by-Step Guide to Custom CNC Machining Orders
Ordering custom CNC machining services may seem daunting, but it’s a straightforward process when broken down into manageable steps. First, identify the specific requirements of your project, including material type, dimensions, and any special features. Next, create detailed design files, such as CAD models, to communicate your vision clearly to the machining service provider. Once your design is ready, submit a request for a quote to multiple CNC machining companies. Comparing quotes will help you find the best fit for your budget and needs. After selecting a provider, work closely with their team to finalize the details and ensure the project stays on track. Finally, review the completed parts for quality and accuracy, providing feedback to the provider for any necessary adjustments.
Real-Life Examples Customized Machining Projects
Customized CNC machining projects span a wide range of industries, each with unique requirements and challenges. For instance, a medical device manufacturer may need highly precise components with biocompatible materials to ensure patient safety. In the automotive industry, custom CNC machining can produce complex engine parts that enhance performance and fuel efficiency. The electronics sector often relies on customized machining to create intricate enclosures and connectors for various devices. One notable example is One Precision’s work in manufacturing custom aluminum keyboard cases. Utilizing 5-axis CNC machines, they produce high-quality, anodized aluminum cases that cater to the specific needs of gaming enthusiasts and professional typists alike.
Enhancing Product Design with Custom CNC Machining
Custom CNC machining not only helps in manufacturing but also plays a crucial role in enhancing product design. By leveraging advanced machining techniques, designers can create intricate geometries and complex structures that are otherwise impossible to achieve. This flexibility allows for greater innovation and creativity in product development. Additionally, custom CNC machining enables rapid prototyping, allowing designers to test and iterate their ideas quickly. This iterative process leads to better-designed products that meet customer needs and expectations. By integrating CNC machining into the design phase, companies can bring their visions to life with unparalleled precision and quality.
Expert Tips for Collaborating with CNC Machining Service Providers
Successful collaboration with CNC machining service providers is key to achieving the desired outcomes for your project. Start by selecting a provider with a proven track record and expertise in your industry. Establish clear communication channels and set expectations from the outset. Provide detailed design files and specifications to ensure the provider understands your requirements fully. Regularly check in on the progress of the project and address any issues promptly. Be open to feedback and suggestions from the provider, as their expertise can often lead to improved results. Lastly, build a long-term relationship with a reliable provider to streamline future projects and ensure consistent quality.
Understanding Different CNC Machining Techniques
CNC machining encompasses a variety of techniques, each suited to different applications and materials. Common methods include CNC milling, turning, and drilling. CNC milling involves using rotary cutters to remove material from a workpiece, creating complex shapes and surfaces. CNC turning, on the other hand, rotates the workpiece while a cutting tool removes material, making it ideal for cylindrical parts. CNC drilling is used to create precise holes in a workpiece. Advanced techniques like 5-axis CNC machining offer even greater flexibility, allowing for the creation of highly intricate and detailed parts. Understanding these techniques helps in selecting the right method for your project.
Selecting the Right Materials for Your CNC Machining Project
Choosing the right material is crucial for the success of any CNC machining project. Factors to consider include the material’s mechanical properties, such as strength, hardness, and corrosion resistance. Common materials used in CNC machining include aluminum, steel, brass, and plastics. Each material has its own advantages and limitations. For example, aluminum is lightweight and corrosion-resistant, making it ideal for aerospace and automotive applications. Steel offers high strength and durability, suitable for heavy-duty components. Brass provides excellent machinability and electrical conductivity, perfect for electrical connectors. Plastics offer versatility and cost-effectiveness for a wide range of applications. Selecting the appropriate material ensures optimal performance and longevity of the final product.
Ensuring Quality Control in Custom CNC Machining
Quality control is a critical aspect of custom CNC machining. It ensures that the final parts meet the specified tolerances and requirements. Implementing rigorous quality control measures throughout the machining process helps identify and rectify any issues early on. Techniques such as coordinate measuring machines (CMM) and optical inspection systems provide precise measurements and detect defects in the parts. Additionally, working with experienced machining service providers who adhere to industry standards and certifications enhances the reliability and consistency of the final product. Regular audits and inspections further ensure that the machining process remains in compliance with quality standards.
The Role of Surface Finishing in Custom CNC Machining
Surface finishing is an essential step in custom CNC machining that enhances the appearance, functionality, and durability of the final product. Common surface finishing techniques include anodizing, powder coating, and plating. Anodizing creates a protective oxide layer on the surface of aluminum parts, improving corrosion resistance and allowing for various color options. Powder coating applies a durable, decorative finish to the part, available in a wide range of colors and textures. Plating, such as nickel or chrome plating, adds a layer of metal to the part’s surface, enhancing its wear resistance and aesthetic appeal. Selecting the appropriate surface finish ensures the final product meets both functional and aesthetic requirements.
The Future of Custom CNC Machining
The field of custom CNC machining continues to evolve, driven by advancements in technology and materials. Innovations such as additive manufacturing (3D printing) and hybrid machining, which combines subtractive and additive processes, are expanding the possibilities of CNC machining. These technologies enable the creation of even more complex and intricate parts with greater efficiency and precision. Additionally, the integration of artificial intelligence and machine learning into CNC machining processes is improving automation and reducing production times. As these advancements continue to develop, custom CNC machining will remain at the forefront of manufacturing, offering unparalleled capabilities and opportunities for innovation.
In conclusion, customizing CNC machining services to meet your specific needs offers numerous advantages, from improved precision and quality to cost savings and enhanced product design. By understanding the different machining techniques, selecting the right materials, ensuring quality control, and leveraging surface finishing options, businesses can achieve exceptional results. Collaborating effectively with CNC machining service providers further enhances the success of custom projects. As technology continues to advance, the future of custom CNC machining holds even greater potential for innovation and efficiency. To stay ahead in the competitive manufacturing landscape, consider exploring the possibilities of customized CNC machining for your next project.
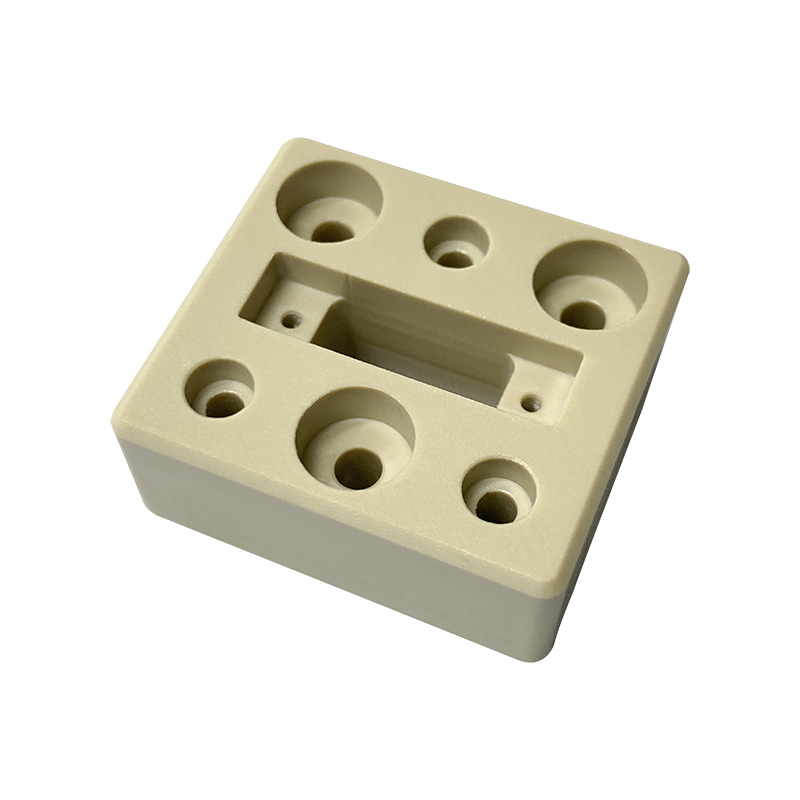
Comments
Post a Comment